Comment les pièces automobiles en fibre de carbone sont fabriquées à l’aide d’un autoclave
La production de fibre de carbone Pièces automobiles L’utilisation d’un autoclave est un processus sophistiqué qui garantit une résistance élevée et des caractéristiques de légèreté. Vous trouverez ci-dessous les étapes détaillées de cette méthode de fabrication :
1. Préparation de la couche de fibre de carbone
Le processus commence par la préparation de la couche de fibre de carbone. Le tissu en fibre de carbone ou préimprégné (pré-imprégné de résine) est découpé en formes et tailles spécifiques en fonction de la conception de la pièce. Les couches de fibre de carbone sont soigneusement disposées dans un moule pour obtenir l’épaisseur et les propriétés structurelles souhaitées. Cette étape est cruciale car elle détermine la résistance et les performances de la pièce finale.

2. Chargement dans le moule
Une fois que la couche de fibre de carbone est préparée, elle est placée dans un moule qui définit la forme de la pièce automobile. Le moule est conçu pour résister aux pressions et aux températures élevées à l’intérieur de l’autoclave. Les couches de fibre de carbone sont soigneusement positionnées à l’intérieur du moule pour assurer un bon alignement et éviter tout défaut ou poche d’air.
3. Mise en place dans l’autoclave
Le moule contenant la couche de fibre de carbone est ensuite placé dans l’autoclave. Un autoclave est un récipient à haute pression qui peut appliquer à la fois de la chaleur et de la pression. Cette étape est essentielle pour le processus de durcissement de la fibre de carbone.
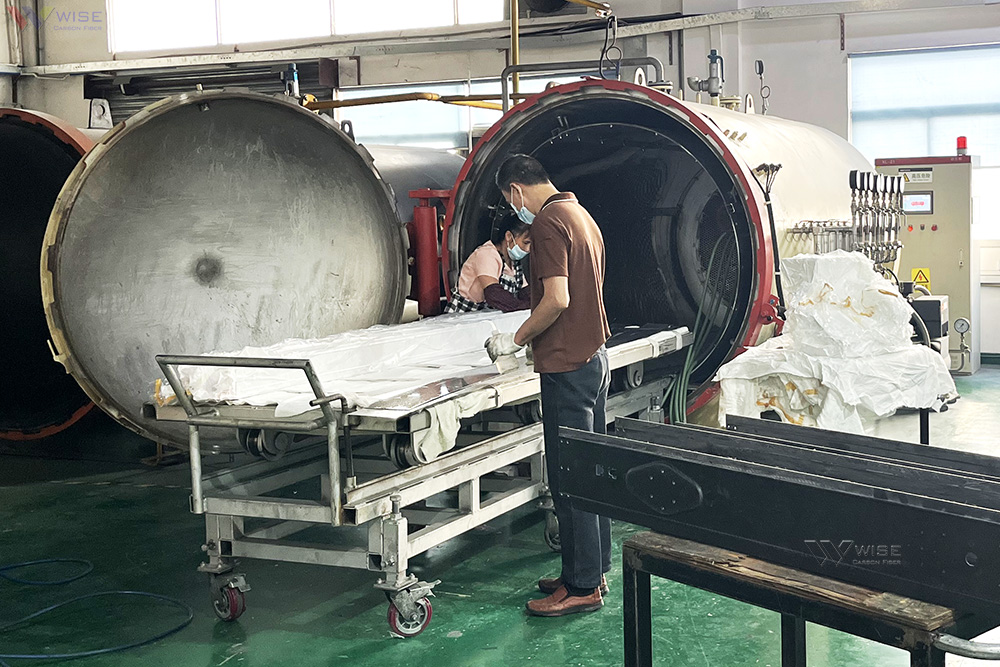
4. Application de chaleur et de pression
À l’intérieur de l’autoclave, la température est progressivement augmentée jusqu’au niveau requis, généralement entre 120 °C et 180 °C (248 °F à 356 °F), selon le système de résine utilisé. La pression est également augmentée, allant généralement de 50 psi à 100 psi. La combinaison de la chaleur et de la pression permet à la résine de s’écouler et d’imprégner complètement la fibre de carbone, assurant ainsi une liaison solide entre les fibres.
5. Processus de durcissement
Le processus de durcissement consiste à maintenir la température et la pression pendant une durée déterminée, généralement plusieurs heures. Pendant ce temps, la résine subit une réaction chimique qui la fait durcir et durcir, formant un matériau composite solide. L’environnement contrôlé à l’intérieur de l’autoclave garantit que le processus de durcissement est uniforme, ce qui permet d’obtenir une pièce de haute qualité avec des propriétés mécaniques optimales.
6. Refroidissement et démoulage
Une fois le processus de durcissement terminé, l’autoclave est progressivement refroidi à température ambiante. Le moule est ensuite retiré de l’autoclave et la pièce en fibre de carbone durcie est soigneusement retirée du moule. Cette étape demande de la précision pour ne pas endommager la pièce.
7. Finition et inspection
La dernière étape comprend la finition et l’inspection. La partie en fibre de carbone est taillée pour éliminer tout excès de matière et atteindre les dimensions précises requises. Il est ensuite inspecté pour détecter tout défaut ou incohérence. Des méthodes de contrôle non destructif, telles que l’inspection par ultrasons, sont souvent utilisées pour garantir l’intégrité de la pièce.

Conclusion
L’utilisation d’un autoclave dans la production de pièces automobiles en fibre de carbone garantit la plus haute qualité et les meilleures performances. Le processus implique une préparation méticuleuse, une application précise de la chaleur et de la pression, ainsi qu’une inspection approfondie, ce qui permet d’obtenir des pièces solides, légères et idéales pour les applications automobiles hautes performances.
WISE a 12 ans d’expérience dans le moulage de fibres de carbone, a une riche réserve technique, vous pouvez nous faire confiance pour prendre en charge votre projet et n’hésitez pas à Personnaliser votre produit.
1. Préparation de la couche de fibre de carbone
Le processus commence par la préparation de la couche de fibre de carbone. Le tissu en fibre de carbone ou préimprégné (pré-imprégné de résine) est découpé en formes et tailles spécifiques en fonction de la conception de la pièce. Les couches de fibre de carbone sont soigneusement disposées dans un moule pour obtenir l’épaisseur et les propriétés structurelles souhaitées. Cette étape est cruciale car elle détermine la résistance et les performances de la pièce finale.

2. Chargement dans le moule
Une fois que la couche de fibre de carbone est préparée, elle est placée dans un moule qui définit la forme de la pièce automobile. Le moule est conçu pour résister aux pressions et aux températures élevées à l’intérieur de l’autoclave. Les couches de fibre de carbone sont soigneusement positionnées à l’intérieur du moule pour assurer un bon alignement et éviter tout défaut ou poche d’air.
3. Mise en place dans l’autoclave
Le moule contenant la couche de fibre de carbone est ensuite placé dans l’autoclave. Un autoclave est un récipient à haute pression qui peut appliquer à la fois de la chaleur et de la pression. Cette étape est essentielle pour le processus de durcissement de la fibre de carbone.
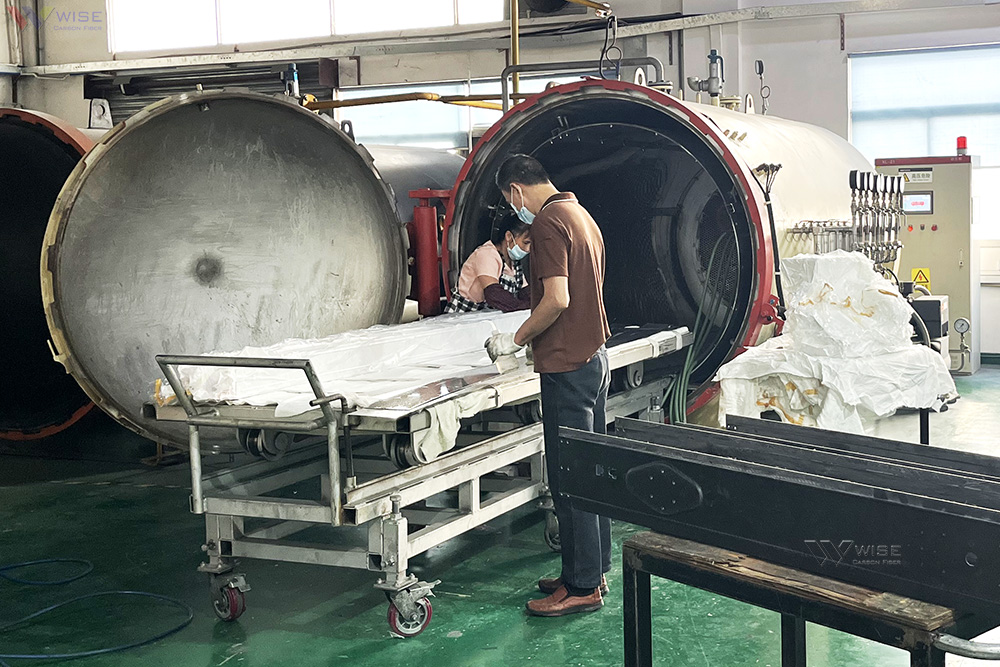
4. Application de chaleur et de pression
À l’intérieur de l’autoclave, la température est progressivement augmentée jusqu’au niveau requis, généralement entre 120 °C et 180 °C (248 °F à 356 °F), selon le système de résine utilisé. La pression est également augmentée, allant généralement de 50 psi à 100 psi. La combinaison de la chaleur et de la pression permet à la résine de s’écouler et d’imprégner complètement la fibre de carbone, assurant ainsi une liaison solide entre les fibres.
5. Processus de durcissement
Le processus de durcissement consiste à maintenir la température et la pression pendant une durée déterminée, généralement plusieurs heures. Pendant ce temps, la résine subit une réaction chimique qui la fait durcir et durcir, formant un matériau composite solide. L’environnement contrôlé à l’intérieur de l’autoclave garantit que le processus de durcissement est uniforme, ce qui permet d’obtenir une pièce de haute qualité avec des propriétés mécaniques optimales.
6. Refroidissement et démoulage
Une fois le processus de durcissement terminé, l’autoclave est progressivement refroidi à température ambiante. Le moule est ensuite retiré de l’autoclave et la pièce en fibre de carbone durcie est soigneusement retirée du moule. Cette étape demande de la précision pour ne pas endommager la pièce.
7. Finition et inspection
La dernière étape comprend la finition et l’inspection. La partie en fibre de carbone est taillée pour éliminer tout excès de matière et atteindre les dimensions précises requises. Il est ensuite inspecté pour détecter tout défaut ou incohérence. Des méthodes de contrôle non destructif, telles que l’inspection par ultrasons, sont souvent utilisées pour garantir l’intégrité de la pièce.

Conclusion
L’utilisation d’un autoclave dans la production de pièces automobiles en fibre de carbone garantit la plus haute qualité et les meilleures performances. Le processus implique une préparation méticuleuse, une application précise de la chaleur et de la pression, ainsi qu’une inspection approfondie, ce qui permet d’obtenir des pièces solides, légères et idéales pour les applications automobiles hautes performances.
WISE a 12 ans d’expérience dans le moulage de fibres de carbone, a une riche réserve technique, vous pouvez nous faire confiance pour prendre en charge votre projet et n’hésitez pas à Personnaliser votre produit.